Bond…Kayln Bond
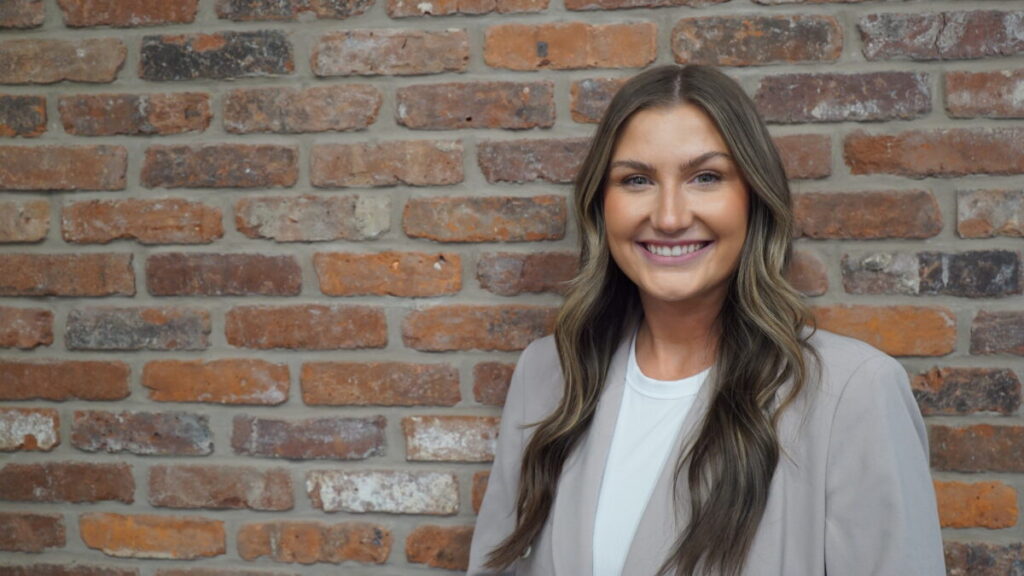
Kayln Bond, Porta Kleen’s material planner, initially applied for another position. “After the interview, Adam Boyden suggested that material planner may be an even better fit. And he was right!” Bond said. “I love the problem-solving aspect of my job. A lot of my job consists of receiving small pieces of information and using those pieces as clues to solve the puzzle.”
As material planner, it’s Bond’s job to source and enter requisitions for all Porta Kleen chemicals, products, service repair parts, PPE and rental equipment for events such as Coachella and Lost Lands. Bond eventually took on the material planner role for all PK and PKX branches except for the maintenance departments.
Bond said a typical day will include entering requisitions for requested parts and researching new parts for equipment repairs. She also maintains the inventory stock for the Porta Kleen warehouse, receives on POs as items arrive and works with invoicing in Basware to ensure vendors are paid.
“In between that, I have been building a visual inventory catalog that will be available in a digital format as well as a hard copy binder for our field employees,” Bond said. “It has all of our common goods, chemicals and repair items.”
Multitasking, critical thinking and self-motivation are some of the skills a material planner must possess. “When I started here, I had zero experience in the industrial work force and I didn’t know a single thing,” Bond said. “But when Matt Foster hired me, he told me, ‘You can teach people information, but you can’t teach them character,’ and I have carried that with me from the beginning.”
Bond believes her background in healthcare administration ahead of working for Porta Kleen gave her the tools she needed to be an effective material planner. “Working in healthcare takes a lot of patience and compassion for people,” she said.
“I think it taught me that every person has a life outside of work that most of the time we don’t know anything about. The standard for healthcare employees and the way they treat their patients is the same way that I view the managers for each department whom I work with every day,” Bond said. “They are my ‘customers’ and I always strive to give them the best outcome.”
Now in her third year, Bond started her position right as the world’s supply chain issues began. “Supply chain issues were the worst in 2021 and 2022,” she said. “This year it has gotten a little better but that also may be due to adjustments in order frequency.”
Bond said minimum order quantities were increased to cover the gap for lead times on chronically backordered items. “In 2022 we had a five-month delay on our truckload of toilet paper, and we had to adapt and change our process to keep from running out,” she said.
Bond was just married November 11 and she and her new husband enjoyed their honeymoon shortly before Thanksgiving. “Outside of that, we both are huge lovers of music, traveling and spending time with our friends, family and our dogs!” she said.